Industrial Projects
Automation through CNC Programming
*CNC machines are the heart of industrial automation*
I worked at Paramount Components Ltd. as a Mechanical Engineer/Programmer, where I streamlined and automated processes by programming various CNC machines for over 2.5 years. Paramount Components Ltd. specializes in sheet metal design and precision fabrication. The precise fabrication of sheet metal products relies heavily on automation through precision-driven CNC machines to ensure that critical product dimensions remain within the 5-10 thousandths of an inch tolerance limits required for the designed specifications. Achieving such fine tolerances is virtually impossible without automation in most cases.
CNC Programming responsibilities:
During my time at Paramount, I programmed various CNC machines for operations such as fiber laser cutting, shear-stress cutting, forming, and bending using both panel benders and press brakes.
A typical CNC programming workflow begins with a CAD model, which serves as the source for generating a DXF (Drawing Exchange Format) file. The DXF file provides geometric data from the design, which is then processed by CAM (Computer-Aided Manufacturing) software to generate the required G-Codes and M-Codes. These codes are programmed on interfaces to drive CNC machines, enabling automated fabrication operations such as cutting, forming, and bending. This process ensures consistent precision while maintaining production efficiency.
CNC Machine Installation Project:
In a CNC Punch Machine (TruPunch 1000 (S19) Type-2) installation project, I collaborated closely with the production team to ensure successful integration and operation of the new machine. The physical installation was handled by the vendor company from which we purchased the machine, but I led the project to integrate programming with the machine and bring it into full operational status.

Stage 1: Customizing Programming Software and Tool Setup
The first stage involved customizing the programming software, BOOST, to make it compatible with our facility’s requirements. This customization included setting up tools, cutting conditions, and raw material specifications.
The company utilizes a variety of tools for both shear cutting and forming operations, such as tapping, countersinks, louvers, dimples, and half-shear operations. Each tool is associated with specific parameters like applied load, lower dead point (LDP), and upper dead point (UDP). To configure these tools, I conducted thorough inspections, reviewed tool specifications, and collaborated with experienced operators.
During this period, I also managed tool refurbishments and disposal as needed, ensuring optimal tool performance. I created a library of over 100 tools by developing CAD models and defining the respective conditions for their use. In addition, I defined the specifications for raw materials—primarily steel, stainless steel, aluminum, and occasionally polycarbonates like Lexan. Properly setting the tool loads was critical for ensuring high-quality operations and prolonging tool life.
Stage 2: Program Creation and Testing:
In the second stage, I developed programs for various operations. These programs were downloaded and tested by a team of production CNC operators. Together, we identified and resolved program failures during machine trials, troubleshooting issues to refine the programming process, tools, and operating conditions.
Safety was a priority throughout this phase. I ensured that all programs leveraged the machine’s built-in safety features. Over the course of several months, we systematically refined the machine’s performance, making it reliable for production. I also created a detailed Standard Operating Procedure (SOP) based on our findings, emphasizing programming techniques for safe and effective machine operation. Additionally, I trained other engineers in CNC machine programming to ensure they could maintain and operate the machine in the future.
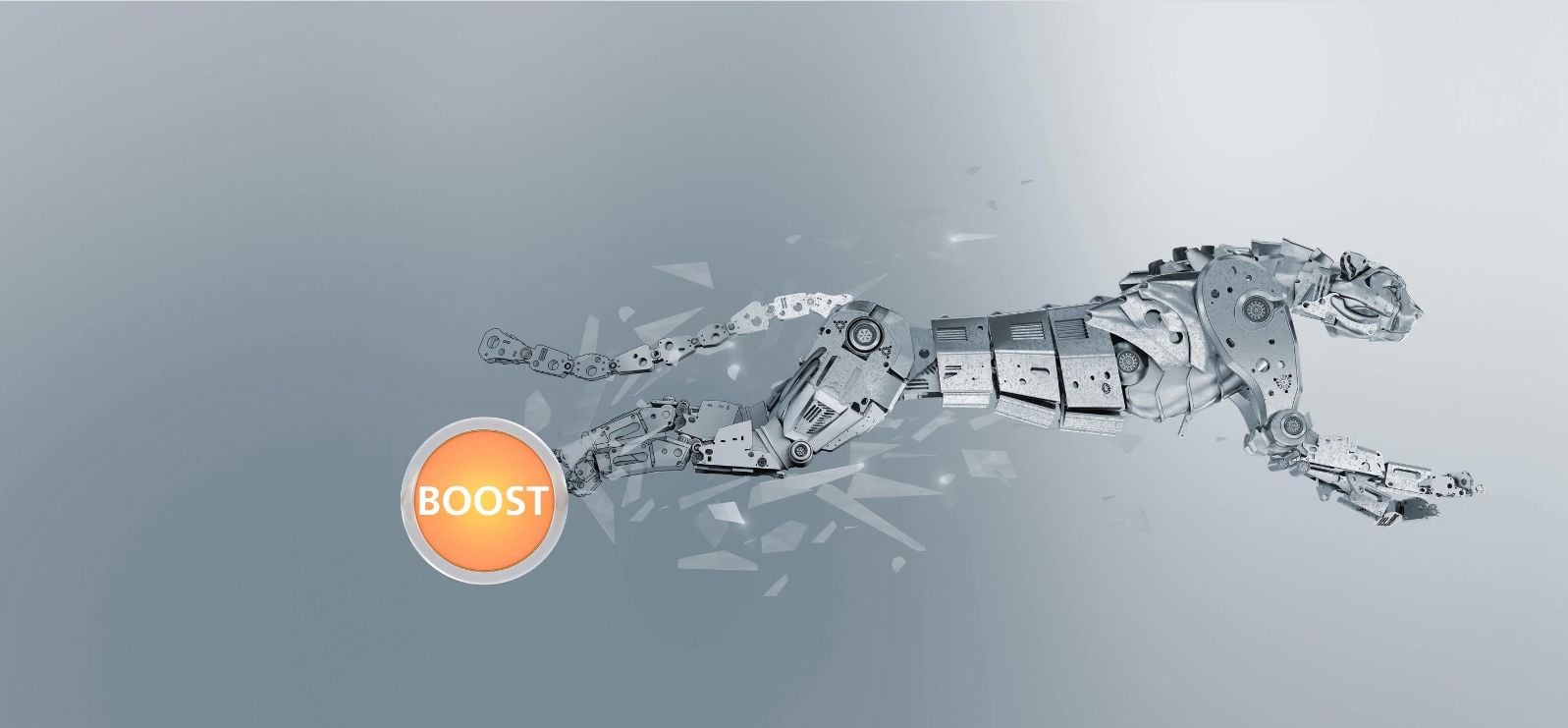
Stage 3: Enhancing Programming Efficiency:
In the final stage, I focused on optimizing the programming process to improve efficiency. This involved selecting the right tools to ensure safe operations with minimal time and cost. Efficient programming required expertise in choosing tools, optimizing cutting paths, and balancing quality with cost-effectiveness.
To further streamline the process, I utilized a feature in the BOOST software that analyzes data from previous programs to suggest optimal tooling combinations and cutting paths. This automation significantly reduced programming time and enhanced overall efficiency.
Through this project, I successfully integrated the CNC Punch Machine into production, ensuring precise, safe, and efficient operation while contributing to the overall productivity of the facility.